I made my first domestic flight to Melbourne this week in 15 months with almost the same level of excitement when I got onto a plane for the very first time a few decades ago – as a little boy. There’s definitely a feeling of lightness as we return to some sort of normalcy, here in Australia, compared to many other countries right now.
After a long day that started at 4am and filled with multiple meetings, I finally got to my accommodation in the evening. I got off the lift on the 4th floor and wanted to find my room (#405). I stared at the visual information that was right in front of me. My tired mind was confused, and I stood there for a few seconds – do I turn left or right? Which way do I turn for room #405? This is visual communication gone totally wrong!
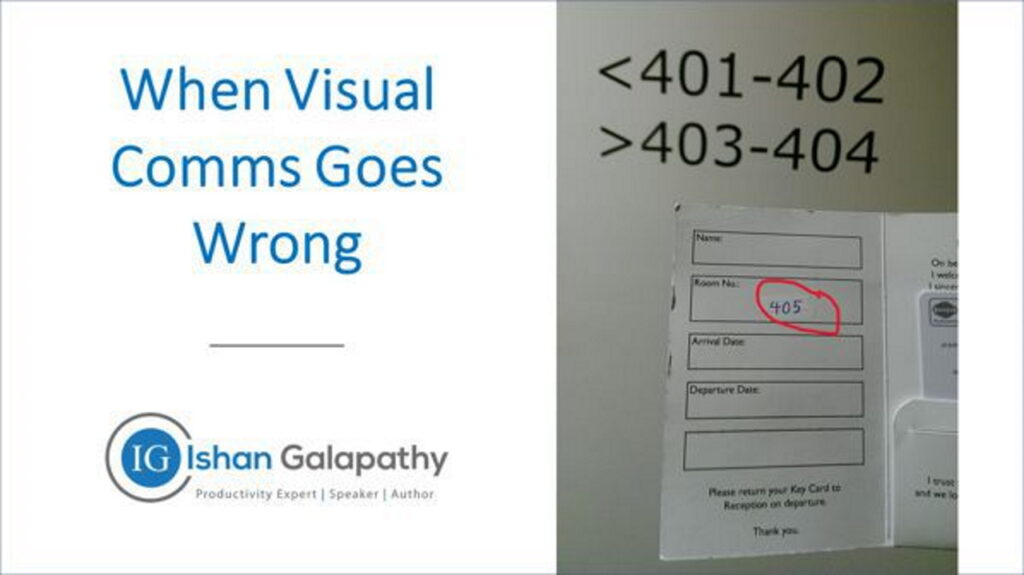
Visual communication is how we actually communicate, we are not reading letters, words and sentences although we think we do. We are merely recognising symbols and then the Neocortex of our brain translates it into something meaningful, based on our education, experiences, upbringing, values etc. I’m not trying to go down a deep philosophical path on visual comms, rather want to explore the impact of this on productivity at work.
In manufacturing, visual communication is one of the ‘go to’ tools for:
Change Management – continuous improvement wouldn’t exist if we couldn’t change processes. So visuals are used effectively communicate process changes to all employees, across all shifts.
Adherence to Standards – everything from lines on the floor marking safe walkways, to machine settings, to hourly output requirements are displayed to ensure that the business produces the finished goods to the right specifications, right standards and safely.
Updates – all the notices that are displayed in various locations; upcoming staff BBQ, new appointments and the advert for the second-hand car that one of the employees is selling etc.
However, it is situations such as the one that I faced when I got off the elevator on the 4th floor, that ends up in costly mistakes in the form of rework, waste, unhappy customers, overtime, frustrated supervisors / managers etc. In these situations, there’s a tendency to think that the ‘root-cause’ is lack of training and the solution to re-train staff associated with that task. It is not the root cause.
The truth is that we have not provided the right information and the right time. Ask yourself:
- Why did the employee / team make that mistake?
- Why wasn’t it obvious?
- Was there too much information confusing the employee?
Don’t make it easier for the employee to do the wrong thing and then blame the employee
for the wrong behaviour / outcome.
PS: Going back to the conundrum with room #405, there was a third path, right behind me next to the elevator, which wasn’t obvious, pointing towards rooms 405-410!